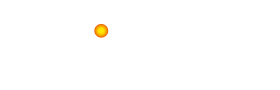
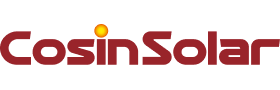
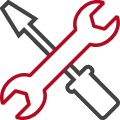
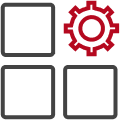
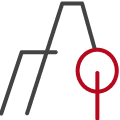
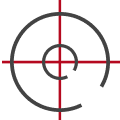
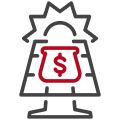
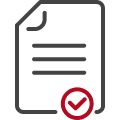
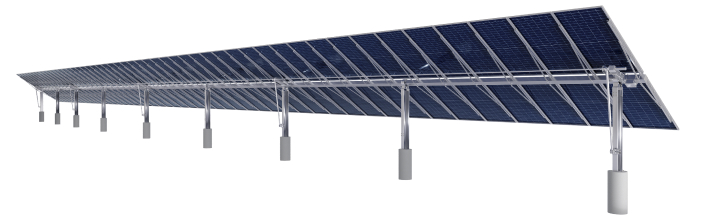
The multi-point parallel drive design has more drive pylons, and the stress distribution of the frame is more uniform, suitable for harsh environmental conditions such as strong winds.
Support mechanical or electrical synchronization hence a more uniform driving torque.
With a hard limit mechanism inside the linear actuator, the overall hard limit and overload protection function is more reliable.
Unique sealing design is applied on linear actuator. Grease lubrication is used hence no oil pollution and no risk of oil leakage.
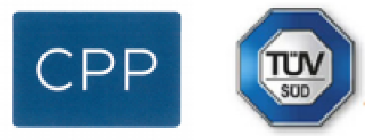
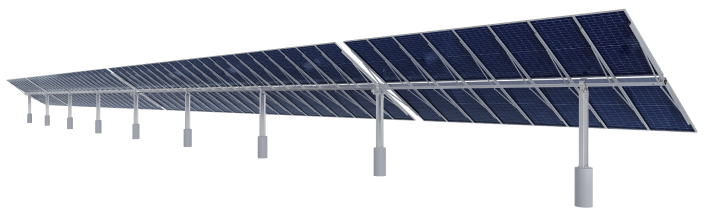
Higher north-south slope adaptability, up to 20%, suitable for larger slope sites.
The slew drive adopts a closed transmission with the worm gear transmitted in a fully lubricated sealed box unaffected by sand and dust, meaning better sand and dust adaptability.
The slew drive can achieve 360-degree rotation, so the slew drive solution has a wider tracking angle range.
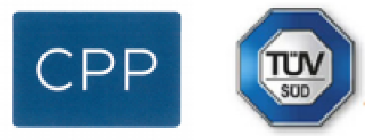
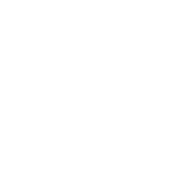
Electrical Synchronization
High Strength Structural Design
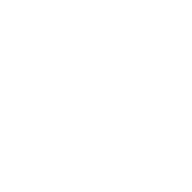
Customized Kinematic Models
Tracking accuracy ≤ 1°
Power Generation Increase 8%-15%
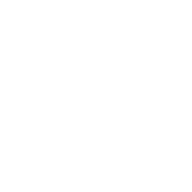
Adapt to Various Applications
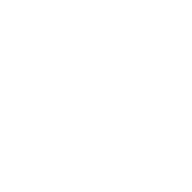
Modular design, easy to assemble and disassemble.
Device self-diagnosis function